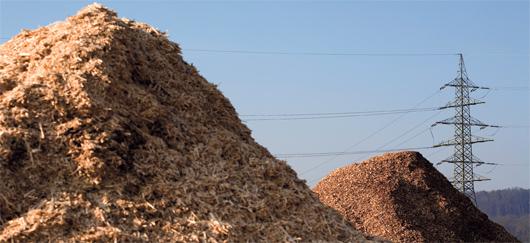
Centrale de gazéification de biomasse à Güssing en Autriche (©EDF-Philippe Eranian)
Définition et usages
La « gazéification » désigne une transformation thermochimique consistant à décomposer par la chaleur un solide combustible carboné (charbon, biomasse) en présence d’un réactif gazeux (gaz carbonique, vapeur d’eau puis oxygène/air) dans le but d’obtenir un mélange gazeux combustible.
La réaction de gazéification se passe dans des conditions de température très élevées (plus de 1 000 °C). Le gaz de synthèse obtenu à la fin, appelé « syngas » (pour « synthetic gas »), est un mélange de deux gaz combustibles : le monoxyde de carbone (CO) et l’hydrogène (H2).
Ce syngas est utilisé principalement :
- comme source de production de chaleur ;
- comme source de production d’électricité par l’action du gaz sur des turbines ;
- comme source de production d’hydrogène, de méthanol et de méthane par traitement chimique ;
- comme source de production de carburant de synthèse par le procédé Fischer-Tropsch.
1 kg de biomasse (bois) permet de produire entre 1 et 1,3 kWh d’énergie électrique et entre 1,7 à 2,5 kWh d’énergie thermique. À titre de comparaison, 1kg de gaz ou du pétrole fournit environ 12 kWh d’énergie thermique.
Processus de gazéification pour production de syngas
Pour parvenir à la production du syngas, plusieurs réactions préalables sont nécessaires. L’ensemble de ce processus est appelé gazéification. Il nécessite, à partir d’une matière organique, d’obtenir au préalable dans le réacteur de la vapeur d’eau (H2O), du carbone (C) et de produire une chaleur suffisante pour la réaction finale de gazéification.
Quatre étapes successives, fortement couplées, sont nécessaires, la troisième produisant la chaleur requise par les trois autres.
1ère étape : séchage de la matière pour produire de la vapeur d’eau
Cette étape se déroule à des températures comprises entre 100°C et 160°C. Sous l’effet de la chaleur, l’eau contenue dans la matière organique s’évapore.
Le combustible carboné résultant est sec et de différentes natures (charbon, biomass, etc.). Dans le cas de produits non homogènes, une phase préalable (tri, broyage) est nécessaire avant d’introduire cet intrant dans le gazéifieur.
2e étape : pyrolyse des intrants pour obtenir du coke (résidus de carbone) et des gaz de pyrolyse
Cette étape sans oxygène (anaérobie) se déroule à des températures situées entre 120 °C et 600 °C. Elle est dite « autothermique » car elle ne produit ni ne consomme d’énergie. En augmentant progressivement la température en l’absence d’oxygène, la matière séchée se décompose et les atomes de carbone s’associent entre eux. Il se forme alors :
- du carbone réducteur presque pur (coke ou résidus de carbone) ;
- un mélange de gaz oxydants non-condensables composés majoritairement d’oxyde de carbone (CO) et d’hydrocarbures (CH4) appelés « gaz de pyrolyse » ;
- des goudrons et des matières volatiles condensables issues de vapeurs de composés organiques (acides acétiques, aldéhydes).
3e étape : oxydation des gaz de pyrolyse pour générer une chaleur suffisante à la gazéification
Cette étape se déroule en présence d’oxygène à des températures comprises entre 1 200°C et 1 500°C. Les matières volatiles issues de la pyrolyse s’oxydent. Cette combustion dégage la chaleur nécessaire aux deux étapes précédentes et à l’étape suivante de la gazéification. Elle nécessite un fort apport en oxygène.
4e étape : la réduction ou « gazéification » du carbone pour produire le syngas
Cette étape se déroule à des températures comprises entre 800 °C et 1200° C. Enl’absence d’oxygène, le coke obtenu lors de la phase de pyrolyse réduit la vapeur d’eau et le gaz carbonique obtenus dans l’étape précédente respectivement en hydrogène et en oxyde de carbone pour former du syngas, combustible mélangeant en proportions variables CO et H2.
Schéma du processus de gazéification
Les différents procédés de gazéification
Le choix d'un type de procédé est guidé par la taille de l'installation, le solide combustible carboné utilisé, l'usage du gaz produit et la maturité des technologies.
A co-courant
À co-courant, les différentes étapes de la réaction de gazéification sont successivement réalisées de haut en bas dans le réacteur. La matière organique est d’abord introduite à son sommet. De l’air est injecté à mi-hauteur pour amorcer la combustion et fournir de la chaleur à l’ensemble du réacteur. L’augmentation progressive de la température permet d’obtenir les différentes réactions entrainant les gaz produits vers la zone la plus chaude du réacteur. Le syngas est récupéré au niveau du socle du gazéificateur.
Schéma de gazogène à co courant
A contre-courant
À contre-courant, l’air est injecté à la base du réacteur et le syngas est récupéré sous son sommet, au dessus de la zone de pyrolyse. Les goudrons sont moins nombreux à s’échapper du réacteur et l’encrassement des conduits est donc plus limité.
Schéma de gazogène à contre courant
Lit fixe
Le procédé à lit fixe peut être soit à co-courant soit à contre-courant.
Lit fluidisé statique
Par ce procédé à lit fluidisé statique, les particules sont mises en suspension dans le réacteur par injection à sa base d’un gaz qui va « soulever » les grains. Cela favorise les échanges thermiques et massiques entre le gaz et le solide.
Dans ce type de réacteur, les différents mécanismes de séchage, pyrolyse, combustion ou oxydation ont lieu dans une seule et même zone.
Lit fluidisé entraîné
Le solide combustible carboné est finement pulvérisé dans un jet d'oxygène. La réaction chimique s’effectue à très haute température et à pression élevée. Cela empêche les goudrons et méthane de se former, les gaz produits en sont ainsi exempts. Le rendement en gaz est donc élevé.
Cependant, le procédé à lit fluidisé entraîné nécessite une forte consommation en oxygène. Par ailleurs, le coût de la pulvérisation préalable du solide combustible carboné est élevé, car il faut obtenir une biomasse ou du charbon finement moulu.
Schema de gazogène à lit fluidisé
Enjeux de valorisation énergétique
La gazéification peut être utilisée comme une solution de substitut dans plusieurs domaines.
La valorisation de la biomasse
La technique de gazéification présente un bilan carbone équilibré dans la mesure où elle utilise la biomasse. En effet, dans ce cas, le CO2 rejeté est celui qui a été absorbé par la photosynthèse ayant produit les végétaux gazéifiés.
La valorisation des déchets organiques
La gazéification des déchets se pose aujourd'hui en concurrent de l'incinération car elle présente plusieurs avantages par rapport aux procédés classiques :
- l'élimination des produits de combustion est effectuée directement sur le syngas, alors que l'incinération produit un volume de fumée beaucoup plus important ;
- l'énergie électrique peut être fournie à partir de moteurs et de turbines à gaz, qui sont beaucoup moins onéreux et plus efficaces que le cycle de la vapeur utilisé dans les incinérateurs ;
- la conversion chimique du syngas permet de produire des carburants de synthèse, et pas seulement de l'électricité.
La gazéification du charbon
Comme pour la biomasse, la gazéification du charbon permet de produire du syngas, souvent utilisé pour la production d’électricité par l’action de turbines. Par ailleurs, la liquéfaction indirecte du charbon CTL (Coal To Liquids) par l’intermédiaire de la gazéification du charbon permet d’obtenir des carburants synthétiques.
La valorisation des résidus issus du raffinage du pétrole
Les résidus issus du raffinage du pétrole comme les goudrons, le coke et l'asphalte peuvent être valorisés par un processus de gazéification. Ils peuvent en effet être, à leur tour, convertis en produits utilisables comme l'hydrogène, la vapeur, l'électricité, l'ammoniac et des produits chimiques.
Par ailleurs, les boues de raffinerie peuvent, elles aussi, être gazéifiées. Ainsi, intégrée à la raffinerie de pétrole, la gazéification peut constituer une solution aux problèmes environnementaux liés à l'élimination des résidus et des boues.
Installations dans le monde
Selon SFA Pacific Inc, une entreprise américaine spécialisée dans l’évaluation des ressources environnementales, on recense 329 unités de gazéification dans le monde (1).
L’Europe a une longue expérience de la gazéification héritée des périodes de pénurie en énergie lors des deux guerres mondiales. En France, le projet GAYA associe l’Ademe, le CEA et GDF Suez pour un démonstrateur de production thermochimique d’électricité par biofuel. Dans l'Union européenne, la « bio-électricité » (issue de biomasse solide ou liquide, de biogaz ou de déchets) a généré, en 2010, 121 TWh (dont 28,6 TWh à partir de biogaz), soit 3,6% de la production électrique totale de l'UE (3 333 TWh)(2).
En Afrique, la plupart des gazéifieurs sont situés en Afrique du Sud, où les carburants synthétiques et les produits chimiques sont produis à partir du charbon depuis 1955.
En Amérique du Nord, les produits chimiques, les engrais et l’électricité sont produits par gazéification sur plusieurs sites des Etats-Unis.
En Asie, les installations de gazéification se situent principalement en Inde, en Chine et au Japon. Les pays d’Asie comme la Chine constituent le marché le plus important en termes de capacité installée et de marché potentiel. L’ensemble des pays tropicaux représentent une zone de développement importante qui devrait émerger très rapidement dans les années à venir.
Malgré les atouts qu’elle présente, la gazéification reste encore peu développée dans le monde, ce qui peut s’expliquer par plusieurs raisons :
- l’approvisionnement en matières organiques doit être continu et homogène. C’est en pratique difficilemen réalisable, même si les ressources sont censées être abondantes ;
- pour des raisons de rentabilité économique et d’efficacité énergétique, la distance qui sépare les ressources des unités de gazéification ne doit pas dépasser 50 kilomètres ;
- la technique de gazéification ne suscite pas encore un intérêt suffisant de la part des professionnels ou des acteurs privés susceptibles d’assurer le développement de ce procédé. Elle reste encore mal connue.
L’industrialisation et la structuration du marché de la gazéification nécessitent encore des efforts de financement de programmes de recherche, par les gouvernements notamment. En outre, la gestion des déchets étant du ressort des pouvoirs publics, le choix de la gazéification plutôt que de l’incinération ne peut qu’émaner d’une volonté politique forte.
Enfin, une implication plus marquée de grands acteurs du secteur privé reste nécessaire pour stimuler le développement de la filière.
Selon Enerkem, une entreprise québécoise spécialisée dans la fabrication de biocarburants, il faut au minimum 50 000 tonnes de matières résiduelles par année pour qu’une usine de gazéification soit rentable (4).
Histoire : des essais aux centrales
L’histoire de la gazéification commence avec Sir Charles William Siemens en 1868 dans une communication scientifique faite à Londres.
Mendeleïev, un chimiste russe, reprend le principe de gazéification vingt ans plus tard. En 1912, une première expérience dans une mine est organisée. À la suite de cette expérience, des résultats encourageants sont obtenus mais les travaux sont interrompus par la Première Guerre mondiale.
De 1933 à 1940, des essais commencent en Union soviétique dans cinq stations expérimentales. Mais quelques années plus tard, ces essais sont interrompus par la Deuxième Guerre mondiale.
La diffusion des résultats obtenus en URSS entraîne une prolifération d’expériences un peu partout dans le monde : États-Unis, Grande-Bretagne, Italie, Maroc, Belgique, etc. Cette fièvre retombe toutefois dans les années 1960 face à l’afflux de gaz naturel et de pétrole peu cher en provenance du Moyen-Orient et provoque un effondrement des prix sur le marché de l’énergie. Après cette période d’interruption, les essais reprennent aux États-Unis et en Europe à la suite des deux chocs pétroliers.
Entre 1975 et 1990, la gazéification retrouve une croissance importante après l’embargo de 1973. Depuis les années 1990, les gouvernements américain et européens apportent une aide financière aux projets de gazéification.